Development
The idea is
what counts.
Ideas are unlimited
and feasibility is catching up.
The requirements that plastic products have to satisfy are constantly increasing – demands in terms of performance, complexity, shape and quality are growing all the time. To prevent unnecessary costs under these circumstances, we focus on upfront, detailed analysis and integrated consideration of all development and production steps. You benefit from the company’s entire know-how right from the outset. We then work in close collaboration with you, using this analysis to develop a detailed concept that serves as a basis for the quotation.
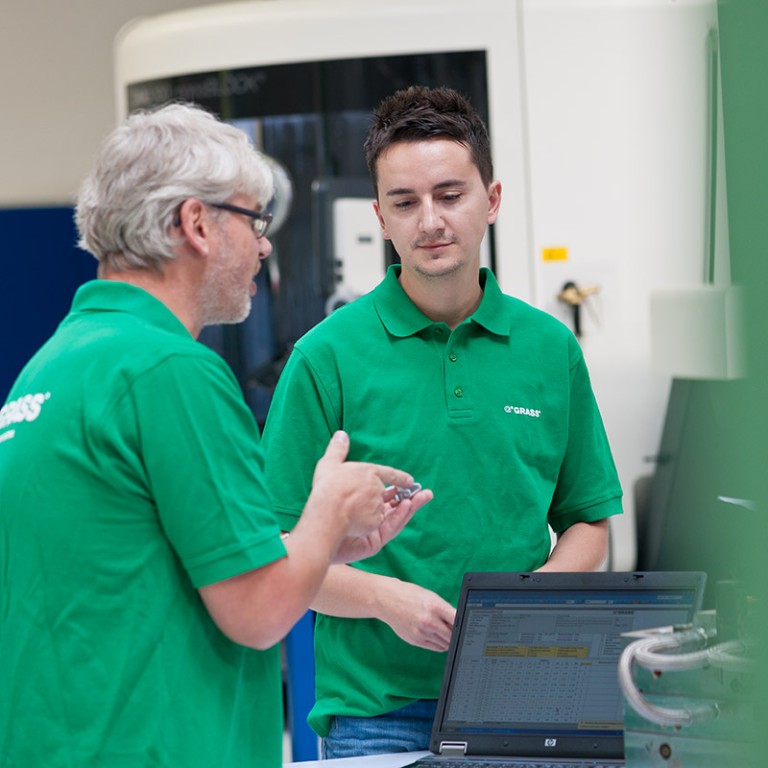
Consultation
Know-how from the outset.
An experienced GRASS project manager is at your side from the first meeting through to the delivery of the series parts. He will be your main contact and coordinates the entire process. You will receive comprehensive support and advice for the design and materials and their combinations as well as for any questions that arise.
Project Management ensures that your product is correctly developed and produced in line with the process. This ensures that the time and cost frameworks are complied with, quality is guaranteed and the product goal is reached.
An idea
becomes reality.
Design
Toolmaking
The cradle
of the product.
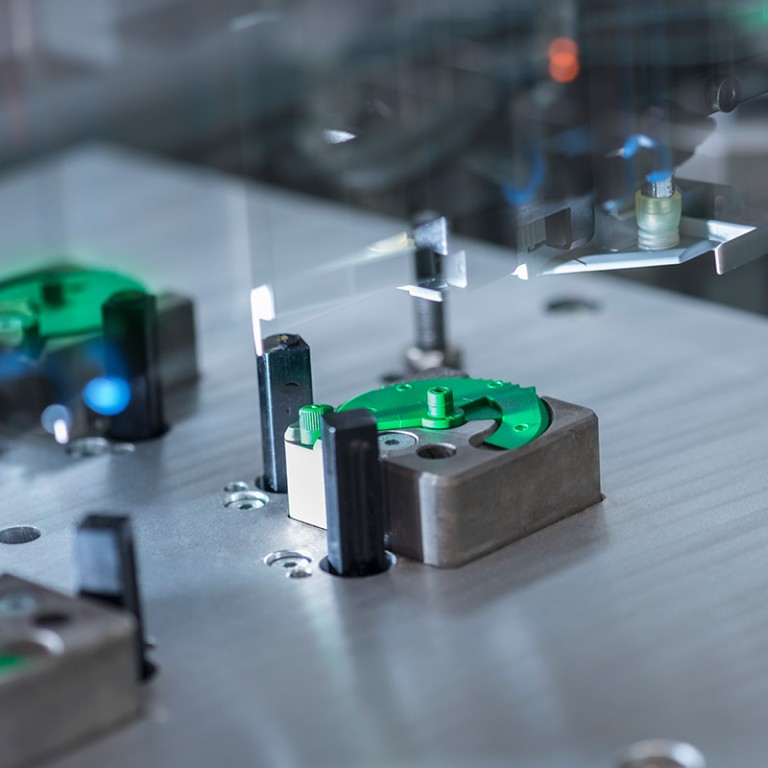
Plastic injection moulding
We get plastics into shape.
At our Salzburg site we have more than 40 microprocessor-controlled plastic injection moulding machines with a clamping force ranging from 50 to 300 tonnes. This comprehensive range of equipment means that we are not restricted to specific mould sizes and also allows us to make micro-injected moulded parts. We create capacities of up to 128 identical moulded parts in one injection moulding cycle. This increases productivity while maintaining a high level of quality.
The machines are operated by a highly-qualified team of experts who have a perfect command of the interaction between flow velocity, pressure and temperature, and who are also keen to experiment.
Metalworking
Combining different materials opens up new possibilities.
As a plastic and metal processing company we are also able to think outside the plastic box when combining materials. The combination of plastic and metal parts is especially advantageous when the properties of both materials are required for a product. As in the case of hybrid vehicles, the advantages of different technologies are used to create added value in the form, function or design.
Assembly
Bringing together
what belongs together.
Solutions for complex applications can often only be achieved with the precise interaction of several components. For this reason we not only produce individual plastic components, but assemble these to create complete assemblies. It is also possible to integrate additional third-party parts into the assembly process. This means you receive professionally assembled and tested functional parts for your end product.
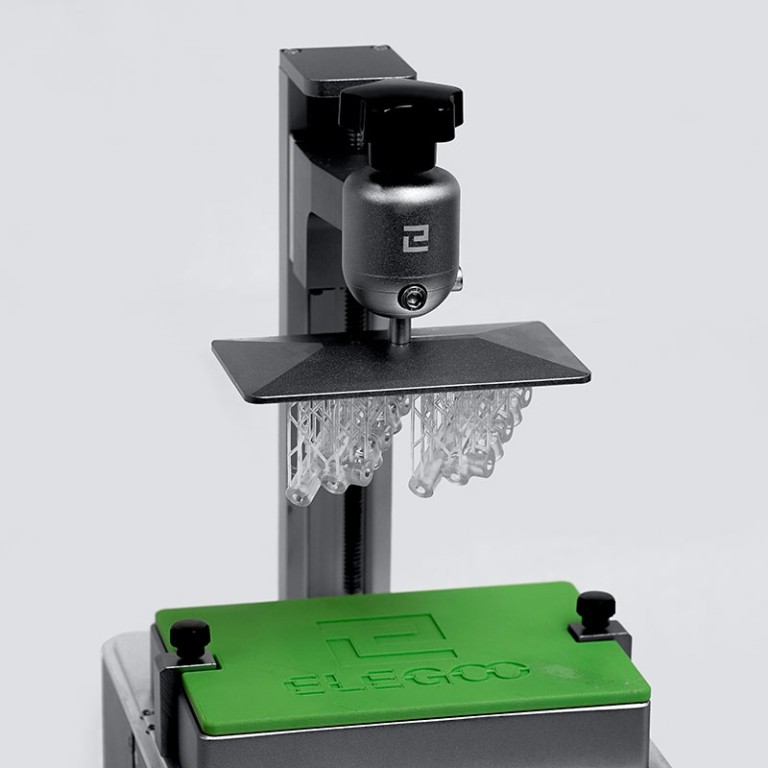
3D printing applications
From prototype to small series.
We currently have four 3D printers with two different technologies in use. That enables us to handle a wide spectrum of very different materials. We achieve the highest precision with a layer resolution of just 0.02mm, while we are no strangers to gas-tight additively manufactured parts. With a maximum build chamber of 200x200x300mm, most parts required for our production are possible. Design, calculation and dimensioning are the task of our specially trained in-house technicians and a large proportion of the additively manufactured parts are used in our production, while contracts for external customers can also be performed at any time.
Quality management
Productivity and quality go hand in hand.